Clean Air ( no water past my filters ) then have extra filter on the back of the unit just in case, and any debreis in my pipes.
Was using 45amps with shielded nozzle then decided to try my fine cuts.
Heres the issue if I use the settings for torch to height distance in the manual I get a positive bevel on all 4 sides of anything I cut, initially I thought this was from my Z not being set up right but If ran with out the torch on and when it dispalys .060 torch to work distance I stop it, and check it with a gauge block its within a couple thousandths so my distance is good. Now I turn my DtHC from my candcnc kit off because bu the time it adjust the cuts are done ( im cutting 3d puzzle butterflys I dled from here from one of the members ) it just acts screwy.
So today I did a .5 wide x 4" long rectangle with a line in the center for a line test. I went from the suggested settings
.060 cut
.150 pierce
Cant remember the delay
at 250IPM
if I lowered the height to .030 or even .020 no bevel, adjusted my speeds and got almost no dross awesome! Then changed back y cut and pierce back and still no dross, figured I was set, I also changed the acceleration rates on my table from 30 all the way to 70 to get of dross coming off of the corners, dam was this thing moving,
Redid my butterfly program with the new settings absoltley no change dross on every side everywhere, I expect some but its to much and way to big of a bevel on 16ga its atleast 10+ degrees and Ive checked rechecked my torch to table and its as square as I can get it prolly not even off a few 1/10ths of a degree if that.
Its obvious thicker stuff cuts better, and I thought it was the water splashing up, so I drained some out of the table, I dont have pics of the parts themselves but Ill get them uploaded here tonite.
Ive also read from Jims postings if theres dross speed up the IPM til you hit the dross free zone, well If I have a dross free part thats rectangular and then I switch to a program thats all curves and arcs and has dross on the entire thing do I need to speed it up more? Seems backwards to the fact I read you cut cirlces holes and radiussed corners at 80% cut speed.
I even notice my cu direction was wrong as I accidently clicked the reverse button in my sheetcam and didnt notice thought that was the ticket Same issue.
And when I get my line test pics up, when its excatly what the manual specs are and I get bevel on both sides my kerf width is correct at the top, and prolly only .010 on the bottom as you can barely slide a sheet a paper in the crack with the fine cut.
Anyways enough rambling heres a vid of what I was cutting although it doesnt show much,
http://www.youtube.com/watch?v=3630-icb ... ture=share
And after I spent about 45mins a piece deburring them as I didnt wanna waste it. so took half the day to get 2 together and tacked together.
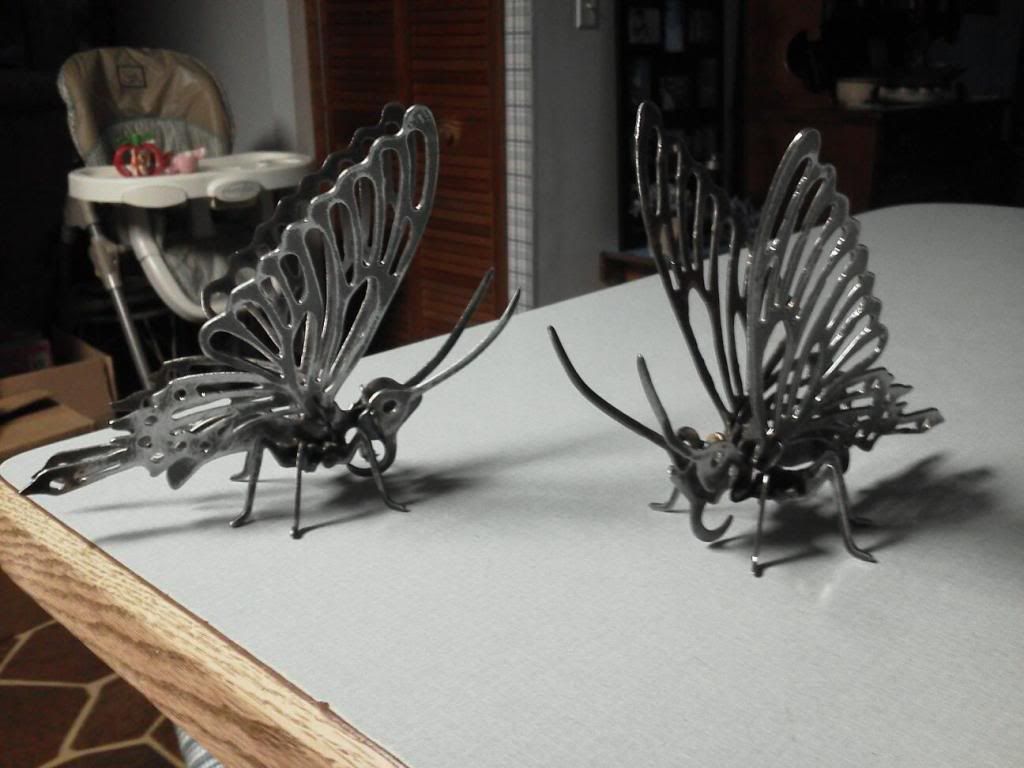